The Future of Manufacturing: Plastic Molding Electrical
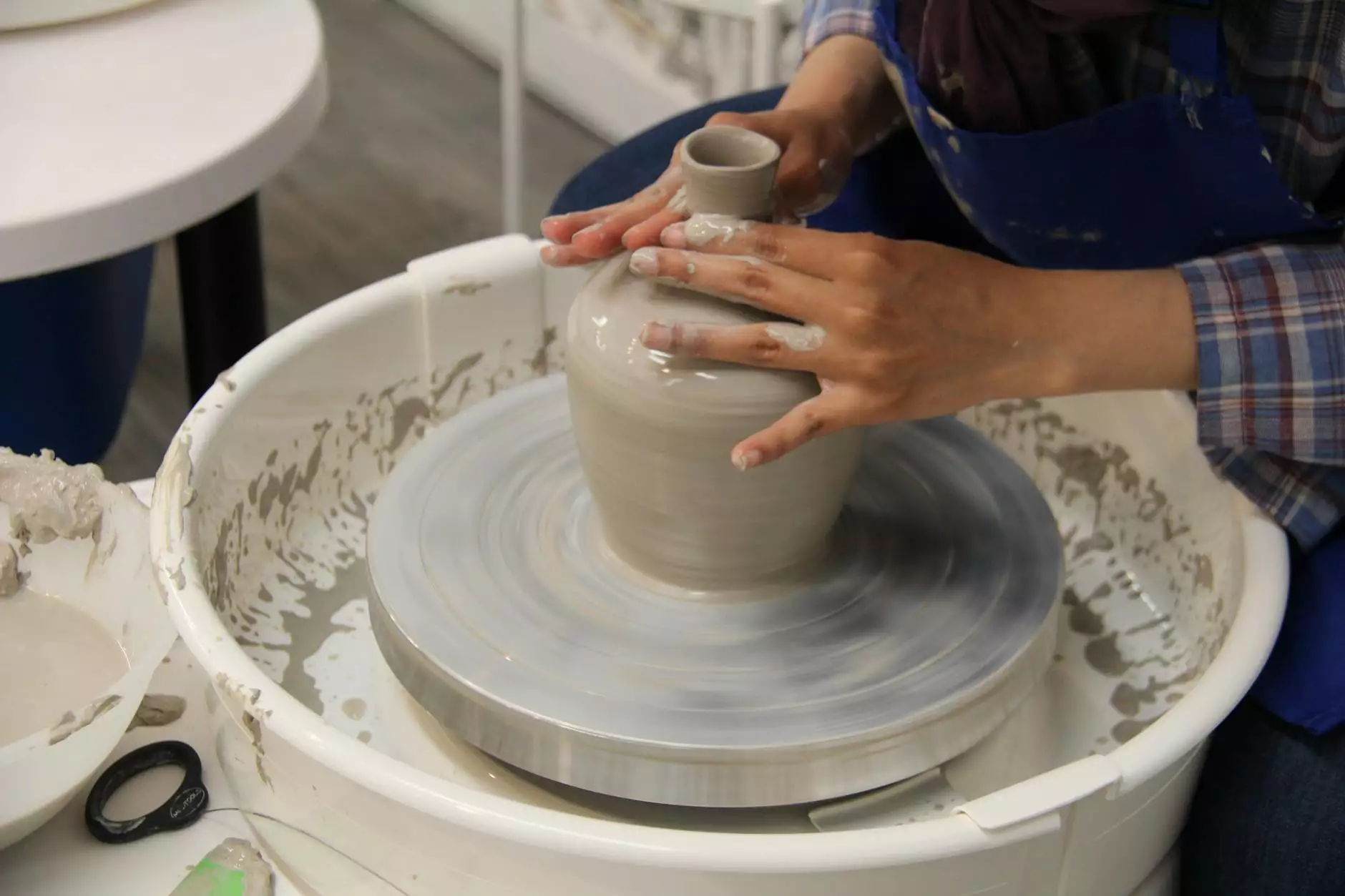
The manufacturing industry has undergone significant changes in recent years, primarily driven by technological advancements and a shift towards sustainable practices. One of the most impactful innovations within this sector is plastic molding electrical. This article delves deep into what this entails, the benefits, applications, and its role in enhancing efficiency while meeting the demands of modern business environments.
Understanding Plastic Molding Electrical
Plastic molding electrical refers to the techniques and processes used to mold plastic materials into specific shapes and designs suitable for various electrical applications. This involves heating plastic until it becomes pliable and then forming it into desired configurations using molds. This method is essential for producing components that are integral to electronic devices and systems.
The Importance of Plastic Molding in the Electrical Sector
In today's world, electrical products are ubiquitous, from household gadgets to complex commercial systems. As such, the need for quality materials and components has never been more critical. Here are a few reasons why plastic molding is vital:
- Cost-Effectiveness: Producing electrical components using plastic molding can significantly reduce costs compared to traditional materials like metal.
- Versatility: Plastic molding allows for a wide range of designs and applications, making it ideal for various electrical equipment.
- Lightweight Design: Plastic components are lighter than metal alternatives, contributing to more efficient products and systems.
- Durability: Advanced plastics can withstand harsh environments and have excellent insulating properties, making them suitable for electrical applications.
Types of Plastic Molding Techniques
Several techniques are employed in plastic molding electrical, each suited to different applications and production needs. Here’s a look at the most common methods:
1. Injection Molding
Injection molding is one of the most widely used plastic molding processes. It involves injecting molten plastic into a mold and allowing it to cool and solidify. This method is favored for its ability to produce complex shapes and high-quality finishes. It's used for various electrical components, such as electrical connectors and housings.
2. Blow Molding
Blow molding is primarily used to create hollow plastic parts, and while it’s less common in the electrical sector, it’s essential for certain applications. For example, plastic battery cases or electronic device enclosures may be created using this method.
3. Extrusion Molding
In extrusion molding, plastic is heated and forced through a die to create long, continuous shapes. This method is commonly used for producing insulating tubes and wiring conduits that are critical in electrical installations.
4. Rotational Molding
Rotational molding is suitable for manufacturing intricate shapes and large parts. It's less frequent in the electrical field but is applicable for large electrical enclosures or casings that need to be both lightweight and robust.
Applications of Plastic Molding Electrical
The applications of plastic molding electrical are vast, touching nearly every aspect of modern life. Below are notable sectors where these techniques are prominently used:
Consumer Electronics
From smartphones to laptops, plastic molded components play a crucial role in consumer electronics. They are used for:
- Enclosures for devices that protect internal components
- Buttons and connectors that facilitate user interaction
- Cooling and insulating elements to enhance performance and safety
Automotive Industry
The automotive sector increasingly relies on plastic-molded parts due to their lightweight and durable nature. Applications include:
- Dashboard components that combine aesthetics with function
- Insulators for electrical systems
- Housing for sensors and electronic control units
Industrial Equipment
Manufacturers of industrial equipment utilize plastic molding electrical techniques to produce components needed for machinery and tools. This includes:
- Protective casings for electrical control panels
- Insulating parts to prevent electrical hazards
- Housing for motors and drives
Medical Devices
In healthcare, precise and reliable electrical components are paramount. Plastic molding is vital for:
- Medical device housings that ensure cleanliness and safety
- Component insulators that protect users from electrical shock
- Parts of diagnostic equipment that require lightweight and durable materials
Advantages of Plastic Molding in Electrical Manufacturing
The transition to plastic molding in manufacturing electrical components presents numerous advantages. Here’s why more companies are embracing this technology:
Efficiency and Speed
Modern plastic molding processes are highly efficient. The ability to create large quantities of parts rapidly reduces lead times and meets market demands swiftly. As businesses strive to remain competitive, speed to market becomes a critical factor.
Enhanced Design Capabilities
Today’s advanced molding technology allows for intricate and innovative designs that were once impossible or too costly to achieve with traditional materials. Designers can experiment with various shapes and features without increasing costs significantly.
Environmental Sustainability
With growing concerns about the environment, industries are looking for ways to reduce their carbon footprint. Plastic molding offers sustainable options, such as the use of recycled materials and energy-efficient processes. This aligns manufacturing with global sustainability goals, helping companies improve their corporate responsibility.
Challenges and Considerations
While plastic molding electrical provides numerous benefits, it is important to recognize the challenges associated with its implementation:
Material Limitations
Not all plastics are equal, and selecting the right material for specific electrical applications is crucial. Manufacturers must consider factors such as heat resistance, electrical conductivity, and durability during their selection process.
Design Constraints
Although advanced molding techniques offer design flexibility, certain limitations still exist. Designers must work within the constraints of the molding process and consider factors like draft angles and wall thickness to ensure manufacturability.
Looking Ahead: The Future of Plastic Molding Electrical
As technology continues to advance, the future of plastic molding in the electrical sector looks bright. With innovations like additive manufacturing, smart materials, and bioplastics emerging on the horizon, the opportunities for enhanced functionality, customization, and sustainability are immense.
Integrating Smart Technologies
The integration of smart technology into molded components is set to revolutionize the industry. By embedding sensors or IoT capabilities into molded products, manufacturers can create smarter, more efficient devices that respond to user needs in real-time.
Environmentally Friendly Innovations
With increasing regulatory pressures and consumer demands for environmentally friendly products, innovations in bioplastics and recyclable materials are gaining momentum. This focus on sustainability will shape the future landscape of plastic molding in electrical manufacturing.
Conclusion
Plastic molding electrical is more than just a manufacturing technique; it’s a crucial driver of innovation across various industries. As businesses like Deep Mould adapt to the evolving landscape and embrace the potential of this technology, they position themselves to lead in efficiency, sustainability, and performance. The benefits are undeniable, and the future is undoubtedly filled with limitless possibilities.