Understanding the Role of China Plastic Injection Mold Manufacturers in Global Industry
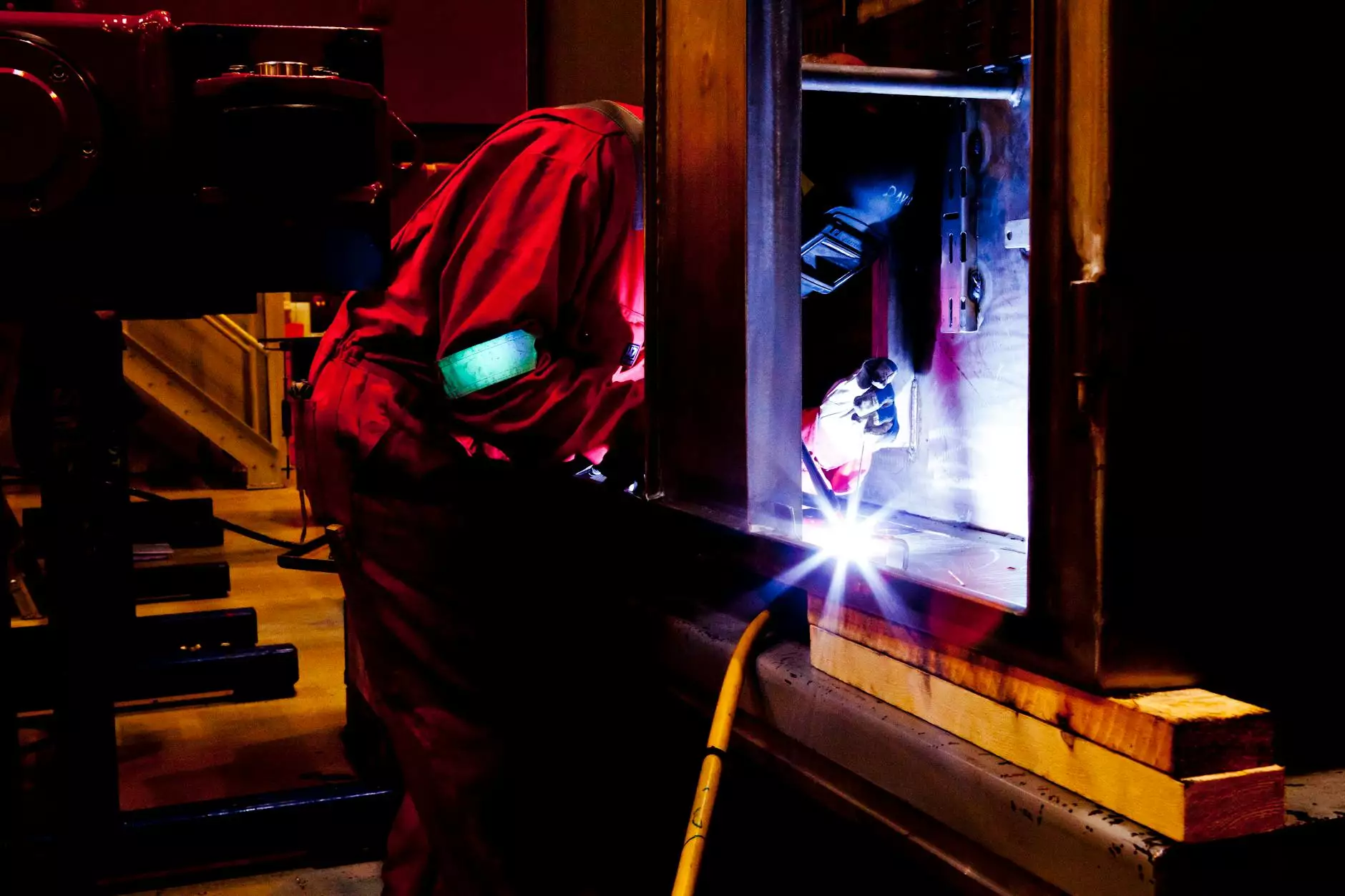
In today's rapidly evolving industrial landscape, plastic injection molding has emerged as a cornerstone of manufacturing processes. Among the key players in this domain are China plastic injection mold manufacturers, who are renowned for their innovation, quality, and cost-effectiveness. This article delves deep into the intricacies of the plastic injection molding process, the factors contributing to the success of Chinese manufacturers, and the impact these companies have on globally integrated supply chains.
What is Plastic Injection Molding?
Plastic injection molding is a manufacturing process that involves the injection of molten plastic into a mold cavity to create highly precise and complex parts. This method is particularly favored for its ability to produce large volumes of uniform products quickly and economically. Here are some key points about this revolutionary process:
- Efficiency: Plastic injection molding is known for its high production rates, making it suitable for mass production.
- Versatility: It can accommodate a variety of materials, including different types of plastics and composites.
- Precision: The process allows for tight tolerances, ensuring that parts fit together accurately.
- Automation: The ability to automate the process enhances productivity and reduces human error.
China's Dominance in Plastic Injection Mold Manufacturing
China has established itself as a leader in the plastic injection mold manufacturing sector. Several factors contribute to this status:
1. Skilled Labor Force
China is home to a vast pool of skilled workers who are well-trained in advanced manufacturing techniques. This workforce is critical in maintaining the high standards of quality that clients expect from China plastic injection mold manufacturers. The combination of traditional craftsmanship and modern technology creates a competitive advantage.
2. Advanced Technology and Machinery
Chinese manufacturers invest heavily in the latest technology and machinery. This commitment to innovation keeps them at the forefront of the manufacturing process, enabling them to produce molds that meet strict international standards.
3. Cost-Effectiveness
One of the most appealing aspects of sourcing from China is the cost-effectiveness. Lower labor costs and operational expenses mean that Chinese manufacturers can offer competitive pricing without sacrificing quality. This is vital for businesses looking to optimize their manufacturing budgets.
4. Strong Supply Chain Network
China's extensive supply chain network facilitates the sourcing of raw materials and components, streamlining the production process. This interconnectedness enhances efficiency and reduces lead times, which is crucial in today’s fast-paced market.
Key Benefits of Partnering with Chinese Manufacturers
Businesses looking to leverage the benefits of China plastic injection mold manufacturers gain numerous advantages:
1. High-Quality Standards
Chinese manufacturers adhere to stringent quality assurance protocols, often exceeding the requirements set by international standards. The implementation of practices such as ISO certification ensures that the molds produced are durable, reliable, and safe for various applications.
2. Customization Capabilities
These manufacturers excel in providing customized solutions tailored to specific client needs. Whether it's a unique design requirement or specialized material usage, China plastic injection mold manufacturers can adapt to meet any challenge.
3. Capacity for Innovation
Continuous investment in research and development keeps Chinese manufacturers at the leading edge of innovation. By leveraging cutting-edge technologies like 3D printing and computer-aided design (CAD), they can enhance the mold-making process, offering clients more efficient and effective solutions.
4. Short Lead Times
Due to their advanced operations, manufacturers in China can produce molds faster than many of their global counterparts. Quick turnaround times are essential for businesses needing to bring products to market rapidly, making China an attractive option for injection molding needs.
The Process of Mold Manufacturing
The journey of creating a plastic injection mold is complex and involves several stages:
1. Design Phase
The first step involves designing the mold using CAD software. Engineers create detailed 3D models that outline all specifications, including dimensions and intended functionality.
2. Material Selection
Choosing the right material for the mold is crucial. Common materials used include steel and aluminium, known for their durability and resistance to wear and tear.
3. Machining
Once designed and materials selected, the machining process begins. Precision equipment is used to carve out the mold's shape, incorporating features like cooling channels and ejection systems.
4. Assembly and Testing
The mold components are assembled, followed by thorough testing to ensure that they meet quality and performance standards. This step is vital in identifying any flaws in the design or construction.
5. Production Phase
After successful testing and adjustments, the mold goes into production. Here, the precise application of injection molding techniques produces the desired parts at scale.
Challenges Faced by China Plastic Injection Mold Manufacturers
Despite their many advantages, China plastic injection mold manufacturers do face challenges:
1. Increasing Global Competition
As more countries develop their manufacturing capabilities, competition becomes fiercer. Chinese manufacturers must continuously innovate and improve to maintain their market leadership.
2. Environmental Regulations
With rising global awareness around environmental sustainability, manufacturers are under pressure to adopt eco-friendly practices. This requires investments in cleaner technologies and processes that can sometimes increase costs.
Environmental Considerations in Mold Manufacturing
In response to the increasing regulatory scrutiny and consumer demand for sustainability, many China plastic injection mold manufacturers are implementing green practices:
1. Waste Reduction Initiatives
Efforts are being made to minimize waste generation during the manufacturing process, utilizing techniques such as recycling scraps and optimizing material usage.
2. Eco-Friendly Materials
Manufacturers are increasingly adopting biodegradable and recyclable materials for production to meet environmental standards and consumer preferences.
3. Energy Efficiency
The transition towards energy-efficient machinery and processes is underway, helping to decrease the carbon footprint associated with mold production.
Looking Ahead: The Future of Plastic Injection Molding in China
The future of plastic injection molding in China is bright, with numerous opportunities on the horizon:
1. Investment in Automation
The rise of Industry 4.0 is transforming manufacturing. Increased automation will lead to greater efficiency, reduced errors, and higher throughput.
2. Growth in Consumer Markets
As consumer demand for diverse products continues to grow, so will the need for innovative molding solutions. Chinese manufacturers are well-positioned to cater to these evolving needs.
3. Global Partnerships
Fostering partnerships with global businesses can open new markets for Chinese manufacturers, creating a win-win situation for innovation and growth.
Conclusion
In conclusion, China plastic injection mold manufacturers play a pivotal role in the global manufacturing ecosystem. Their commitment to quality, innovation, and cost-effectiveness makes them formidable partners for businesses around the world. As they navigate challenges and embrace future trends, it is clear that these manufacturers will continue to be at the forefront of the industry, delivering excellence in plastic injection molding.
For more insights into how China plastic injection mold manufacturers can enhance your business operations, visit deepmould.net. Embrace the future of manufacturing today!