The Ultimate Guide to **Fitting Lubrication**
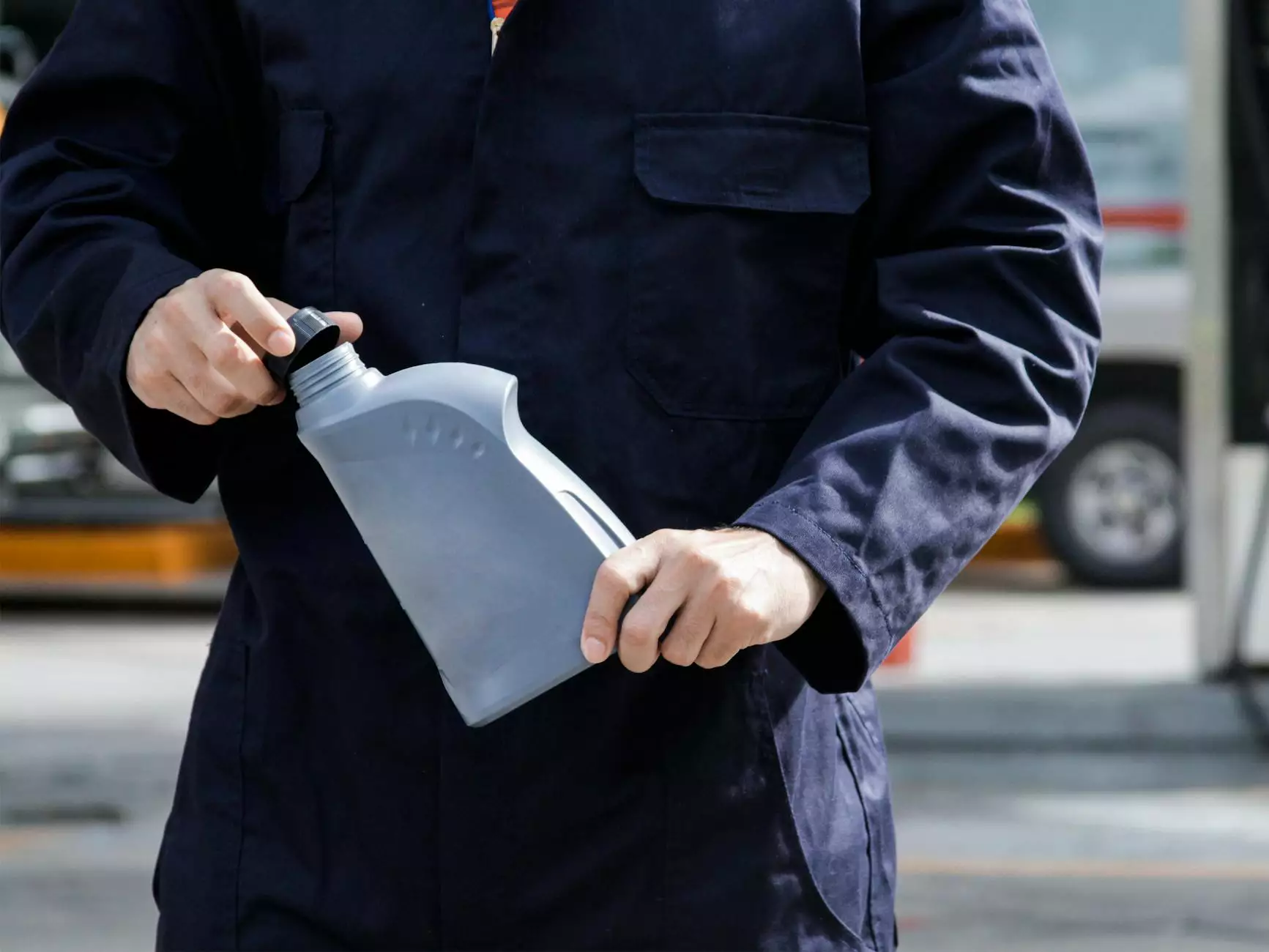
In the world of industrial maintenance and equipment longevity, fitting lubrication plays a pivotal role. Fittings are essential components in various systems, ensuring smooth operations in mechanical applications. This guide delves deep into the importance of lubrication, types of lubricants, applications, and best practices to keep your fittings in optimal condition.
Understanding Fitting Lubrication
Fitting lubrication refers to the application of lubricants to fittings to minimize friction, reduce wear, and prevent corrosion. Proper lubrication not only enhances the operational efficiency of fittings but also significantly extends their lifespan. In industrial settings, neglecting this crucial aspect can lead to catastrophic failures, increased downtime, and costly repairs.
The Importance of Fitting Lubrication
Why is fitting lubrication so critical? Here are several reasons:
- Reduced Friction: Lubricants create a film between moving parts, significantly reducing friction and wear.
- Corrosion Prevention: Quality lubricants protect metallic surfaces from oxidizing agents, which can cause rust and corrosion.
- Heat Reduction: By minimizing friction, lubricants also help in dissipating heat generated by moving parts, preventing overheating.
- Noise Reduction: Lubricated fittings operate more smoothly, leading to a decrease in operational noise.
- Enhanced Equipment Life: Regular lubrication significantly increases the life expectancy of fittings and connected components.
Types of Lubricants Used for Fittings
There are various types of lubricants used in the lubrication of fittings, each serving different purposes:
1. Grease
Grease is a semi-solid lubricant formed by mixing oil with thickening agents. It’s ideal for applications where long-lasting lubrication is required. Grease is water-resistant and adheres to surfaces better than liquid lubricants, making it suitable for outdoor fittings.
2. Oil
Liquid oils are versatile and can be used in various fittings. They are excellent for high-speed applications as they flow more readily, providing quick lubrication. However, they require more frequent reapplication compared to grease.
3. Dry Lubricants
Dry lubricants, such as graphite or molybdenum disulfide, provide lubrication without leaving a messy residue. They are often used in applications where oil or grease may attract dirt and debris.
Choosing the Right Fitting Lubrication Method
Selecting the right lubricating method and product is crucial for optimal performance. Consider the following factors:
1. Operating Environment
Evaluate whether the environment is prone to extreme temperatures, humidity, or contaminants, as this will affect the choice of lubricant.
2. Load and Speed Conditions
Understand the load-bearing capacity and speed of the fitting mechanism. High-speed applications may require a liquid lubricant while heavy-load fittings might benefit from grease.
3. Compatibility
Ensure that the selected lubricant is compatible with the materials of the fittings. Using incompatible lubricants can lead to degradation and failure.
Best Practices for Fitting Lubrication
To achieve maximum effectiveness, it's essential to follow best practices in fitting lubrication:
1. Regular Maintenance Schedule
Create a maintenance schedule that includes periodic cleaning and lubrication of fittings. Regular checks can prevent excessive wear and identify potential issues early.
2. Proper Application Techniques
Utilize appropriate application techniques. Avoid over-lubrication, which can lead to excess buildup and attract dirt, and under-lubrication, which can cause damage due to friction.
3. Use Quality Lubricants
Only use high-quality lubricants that meet the industry standards and specific requirements of your fittings. Discount or substandard products can lead to catastrophic failures.
Consequences of Poor Fitting Lubrication
Neglecting proper lubrication can lead to several detrimental effects on fittings:
1. Increased Wear and Tear
Friction without lubrication leads to excessive wear, ultimately necessitating replacement.
2. High Operating Costs
Frequent repairs and replacements due to poor lubrication can inflate operational costs, making it an expensive oversight.
3. Downtime
Equipment failure due to inadequate lubrication results in costly downtime, disrupting productivity and workflows.
The Future of Fitting Lubrication
As technology advances, innovations in lubrication are emerging. Smart lubricants equipped with sensors are capable of monitoring performance and usage, alerting maintenance teams when lubrication is needed. This level of technology enhances reliability and efficiency in industrial settings.
Embracing Automation
Automated lubrication systems are becoming increasingly prevalent, providing precise and timely lubrications without human intervention. These systems can be programmed to deliver the right amount of lubricant at the right time, further enhancing the lifespan and performance of fittings.
Conclusion
In summary, fitting lubrication is not merely an optional maintenance task—it is a crucial aspect of mechanical integrity and efficiency. By understanding the importance of lubrication, choosing the appropriate materials, applying them correctly, and keeping up with maintenance schedules, businesses can optimize performance and extend the life of their fittings. Investing time and resources in proper lubrication practices can lead to significant savings and enhanced productivity in the long run.
For premium quality fittings and expert advice on fitting lubrication, visit us at fitsch.cn. Our dedicated team is ready to assist you in achieving operational excellence.