Understanding **Plastic Injection Molding**: The Backbone of Modern Manufacturing
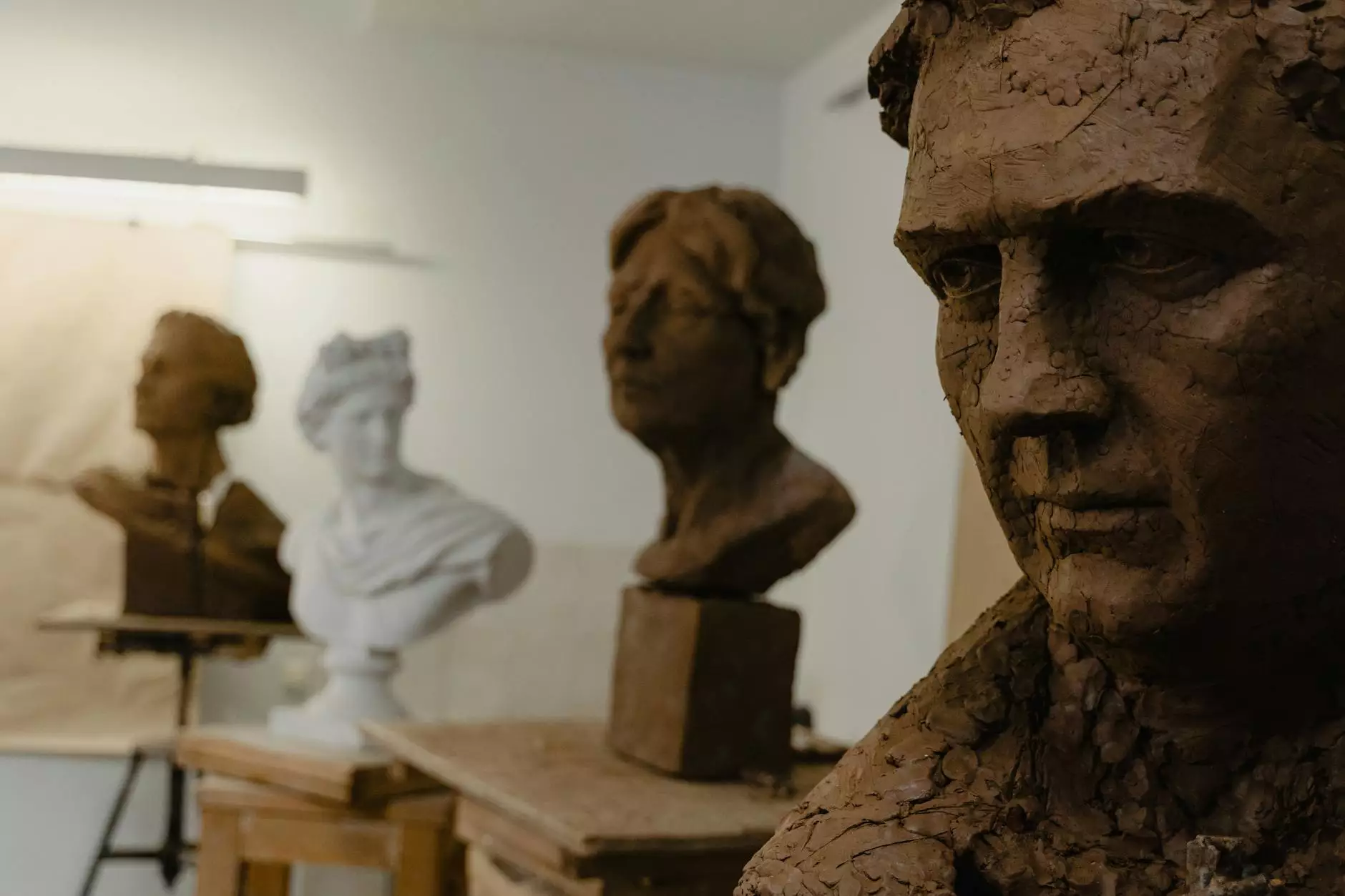
In today's rapidly evolving manufacturing landscape, plastic injection molding stands out as a pivotal process that enables the creation of high-quality, complex plastic parts efficiently and cost-effectively. This comprehensive guide delves into the intricacies of plastic injection molding, highlighting its significance in various industries, including how businesses like DeepMould.net thrive in this competitive environment.
What is Plastic Injection Molding?
At its core, plastic injection molding is a manufacturing process used for producing parts by injecting molten material into a mold. This method is particularly beneficial for creating plastic products with intricate designs and high precision. The process is widely appreciated for its efficiency, speed, and scalability, making it a favorite among manufacturers looking to meet large-scale production demands.
How Does the Plastic Injection Molding Process Work?
The process of plastic injection molding involves several critical steps, each contributing to the final quality of the product:
- Designing the Mold: The first step in the injection molding process is designing the mold, which can be a complex undertaking requiring advanced engineering skills and software.
- Heating the Plastic: The selected plastic material (pellets) is heated until it reaches a molten state, making it pliable for injection.
- Injecting the Material: The molten plastic is injected into the mold at high pressure. This step requires precision and control to ensure the material completely fills the mold cavity.
- Cooling and Solidifying: Once the mold is filled, it is cooled to allow the plastic to solidify, taking on the desired shape.
- Mold Release: After cooling, the mold opens, and the finished part is ejected, ready for further processing or assembly.
Benefits of Using Plastic Injection Molding
Businesses across various industries leverage plastic injection molding for several reasons. Here are some compelling benefits:
- Cost-Effectiveness: Once the initial mold is created, the cost per unit decreases significantly with larger production volumes.
- Speed and Efficiency: The process allows for rapid production of parts, often resulting in shorter lead times.
- Complex Geometries: It enables the creation of intricate shapes and designs that would be difficult or impossible with other manufacturing methods.
- Consistency and Precision: The process provides high levels of accuracy and repeatability, ensuring that each part meets stringent specifications.
Applications of Plastic Injection Molding
Plastic injection molding finds applications in various sectors, making it an invaluable process in modern manufacturing. Some of the major applications include:
- Automotive Components: From dashboard panels to intricate wiring harnesses, the automotive industry extensively uses injection-molded parts.
- Consumer Electronics: Devices like smartphones, tablets, and even appliances often use injection-molded casings and components.
- Medical Devices: High-precision parts for medical devices require the reliability and accuracy that injection molding provides.
- Household Products: Many everyday items, from containers to toys, are produced using this versatile manufacturing method.
The Role of Metal Fabricators in Plastic Injection Molding
Within the plastic injection molding ecosystem, the role of metal fabricators is crucial. They not only design and manufacture molds but also ensure that they are robust enough to withstand multiple production cycles. Here’s how metal fabricators contribute:
- Design and Engineering: Skilled engineers design molds that meet intricate specifications, ensuring optimal production efficiency.
- Material Selection: Fabricators choose materials that provide durability and thermal resistance, crucial for the longevity of the mold.
- Precision Machining: They employ advanced precision machining techniques to create molds that deliver superior performance.
Choosing a Reliable Manufacturer for Plastic Injection Molding
When selecting a manufacturer for plastic injection molding, several factors must be considered to ensure a successful partnership:
- Experience and Expertise: Look for companies with a proven track record and substantial experience in the industry.
- Quality Assurance: Ensure that the manufacturer implements stringent quality control measures to guarantee the integrity of the parts produced.
- Technological Capabilities: A manufacturer equipped with modern technologies can provide better precision and capabilities.
- Customer Testimonials: Feedback from previous clients can offer insights into the company’s reliability and service quality.
Trends Shaping the Future of Plastic Injection Molding
The field of plastic injection molding is continuously evolving. Here are some trends that are currently shaping its future:
- Smart Manufacturing: With advancements in technology, the incorporation of IoT in injection molding allows for real-time monitoring and predictive maintenance.
- Eco-friendly Materials: There is a growing emphasis on using sustainable and biodegradable materials to reduce environmental impact.
- Automation and Robotics: Automation is enhancing production efficiency and precision, making the process faster and reducing the risk of human error.
Conclusion: The Strategic Importance of Plastic Injection Molding
In conclusion, plastic injection molding is an essential process within the manufacturing sector that drives innovation and efficiency across various industries. The benefits, applications, and continual advancements make it a cornerstone for businesses aiming to excel in a competitive market.
As companies like DeepMould.net lead the charge in metal fabrication and molding technologies, the future looks promising for industries that embrace these practices. By understanding and leveraging plastic injection molding, businesses can position themselves for success in an ever-evolving marketplace.