Understanding Injection Mold Tools in the Metal Fabrication Industry
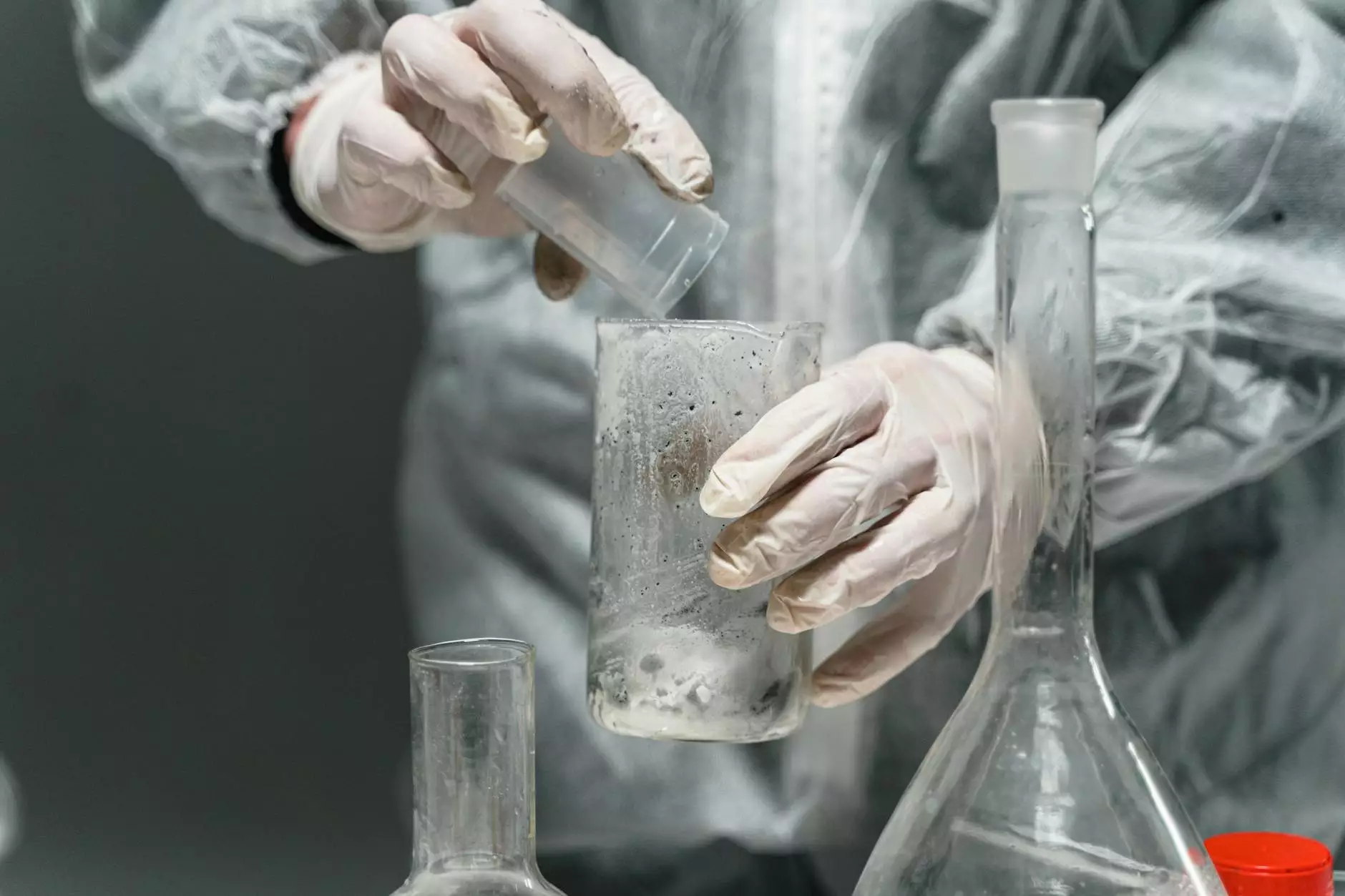
In the competitive world of metal fabrication, the importance of precision and reliability cannot be overstated. One of the critical components that enable manufacturers to achieve these high standards is the use of injection mold tools. These tools play a vital role in shaping and producing high-quality parts efficiently and accurately.
What Are Injection Mold Tools?
Injection mold tools are specialized devices used in the injection molding process to create parts by injecting molten material into a mold cavity. This technique is widely used for manufacturing complex shapes and components in various industries, including automotive, consumer goods, and medical devices.
The Injection Molding Process
The injection molding process involves several key steps:
- Material Preparation: Raw plastic or metal pellets are heated until they melt into a liquid form.
- Injection: The molten material is injected into the mold at high pressure.
- Cooling: The material cools and solidifies within the mold.
- Mold Opening: Once solidified, the mold is opened to eject the finished part.
Advantages of Using Injection Mold Tools
There are numerous advantages to incorporating injection mold tools in your production process:
- Precision: Injection molding provides high accuracy, ensuring that each part meets specifications closely.
- Efficiency: Once the molds are created, production can be scaled rapidly, leading to lower per-unit costs.
- Versatility: Injection mold tools can be used to manufacture various items, from simple components to complex assemblies.
- Consistency: High repeatability allows for uniform parts in large quantities, minimizing variations.
- Material Options: A wide range of materials can be utilized, including thermoplastics, thermosets, and metals.
Types of Injection Mold Tools
There are various types of injection mold tools used in the industry, tailored for specific applications:
1. Single Cavity Molds
These molds produce a single part per cycle. They are ideal for low-volume production or complex geometries.
2. Multi-Cavity Molds
Designed to produce multiple parts simultaneously, these molds increase production rates and reduce costs.
3. Family Molds
Family molds create different parts in a single cycle. This efficiency is advantageous for manufacturers producing a variety of components.
4. Hot Runner Molds
Hot runner molds keep the material in a molten state, reducing waste and cycle time, which is critical for high-volume runs.
The Role of Deep Mould in Injection Molding
At Deep Mould, we specialize in providing top-notch injection mold tools that cater to the needs of various industries. Our commitment to excellence is evident in the quality of our molds and our innovation in the manufacturing process.
Expert Design and Engineering
Our team of engineers collaborates with clients to design molds that meet their specific requirements. We leverage advanced CAD software to simulate the injection molding process and ensure optimal design outcomes.
Quality Materials and Craftsmanship
We use only the highest quality materials for our molds, ensuring durability and longevity. Our precision machining techniques guarantee that every part is crafted to the highest standards.
Challenges in Using Injection Mold Tools
While injection mold tools offer many benefits, there are challenges that manufacturers must address:
- Initial Costs: The upfront investment in mold design and fabrication can be substantial.
- Long Lead Times: Developing highly intricate molds can take time, impacting production schedules.
- Maintenance Requirements: Regular maintenance is necessary to ensure molds operate efficiently over time.
How to Choose the Right Injection Mold Tools
Selecting the appropriate injection mold tools involves considering several factors:
- Part Design: Understand the specifications of the part to determine the mold type.
- Material Compatibility: Ensure that the molds are suited for the materials you plan to use.
- Production Volume: Assess expected production volumes to select between single or multi-cavity molds.
- Budge and Time: Consider your budget and the timeline for production to choose the right tooling solution.
Future Trends in Injection Mold Tools
The field of injection molding is continuously evolving. Emerging trends that will shape the future of injection mold tools include:
1. Advanced Materials
As new materials are developed, injection molds will need to adapt, allowing for greater flexibility and applications.
2. Automation and Robotics
Integrating automation and robotics into the injection molding process will enhance efficiency and precision, reducing labor costs.
3. Environmental Considerations
With a growing emphasis on sustainability, there will be a push for molds that use eco-friendly materials and processes.
Conclusion
In summary, injection mold tools are indispensable in the metal fabrication industry, providing a vital solution for producing high-quality components efficiently. Companies like Deep Mould are at the forefront of this technology, delivering customized solutions that empower manufacturers to excel in their industries.
As you contemplate integrating injection mold tools into your production process, consider the insights shared in this article. Choosing the right mold and understanding the intricacies of the injection molding process can significantly influence your manufacturing success. Reach out to Deep Mould today to explore how we can assist with your injection molding needs!